Industrial Laser Marking Systems / Laser Markers
Laser Marking on Plastic
-
Tags:
- Laser Marking , Laser Etching , Automotive
Plastics vary significantly in their chemical makeup and may respond differently to heat or to laser marking processes such as etching and engraving, so to get optimal results its necessary to select a machine compatible with your specific material and requirements.
Direct Part Laser Marking on Plastic Parts
Laser marking is a reliable and cost-effective technique often used to mark plastic parts. By precisely laser etching plastic surfaces, this equipment produces permanent, high-quality marks. These markings also cause minimal distortion and are resistant to chemicals, abrasion, and extreme temperatures. Common plastics laser-marked include ABS, epoxy, and PET. When laser marking plastic products, the laser light does not penetrate the material. Instead, it chemically or thermally changes its surface according to the laser power intensity within the beam of light.
Laser markings may typically be seen in applications such as brand logos engraved on various appliances and portable electronics, part numbers printed on automotive parts such as brake calipers, or serial numbers etched onto medical tools. As a valuable tool for personalisation and customisation, laser marking plastic has proven to be a valuable option for manufacturers across numerous industries.
Discover more about this product.
Click here to book your demo.

Types of Laser Marking Machines for Plastic
Laser marking plastic differs from other materials because of plastic’s heat properties. When plastic is exposed to heat, it traps it. By trapping the heat, it can cause distortions or swelling from heat sensitivity. Because of this, laser marking plastic requires a laser marking machine that applies minimal heat. This can either be a UV or a hybrid laser marking machine.
UV Laser Marker
UV lasers are used for laser marking plastic because they mark with a process called “cold marking.” Because they operate at a much shorter wavelength than standard lasers (355 nm vs 1064 nm), they are able to process the surface of the material without heat. This provides a higher level of contrast without any damage to the material.
Hybrid Laser Marker
Hybrid laser marking machines use a combination of a YVO4 laser and a fibre laser for laser marking plastic. Together, these lasers make a 1064 nm wavelength with a short pulse and 200kW peak power. The drastically higher peak power allows for high quality marking without the thermal damage that often results from a standard fibre laser.
CO2 Laser Marker
CO2 laser markers use a high level of heat to “melt” the surface of materials, creating a raised or etched mark. This method does not rely on colour contrast but provides durable, permanent marking on plastic in addition to wood, ceramic, and other materials. CO2 laser marking is commonly used for product branding and identification across a range of industries.
We’re here to provide you with more details.
Reach out today!
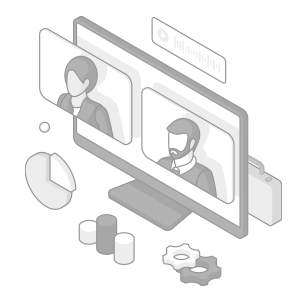
Dark Marking on Plastic
Dark marking on plastic is created by using laser radiation on typically lighter-coloured plastics to create beautiful, vivid contrasting markings. By using this technique, damage from marking the target is minimised.
White Marking on Plastic
White marking on plastic is created by using laser radiation on typically darker-coloured plastics to create equally attractive and contrasted markings. Likewise, damage from marking the target is minimised using this technique.
White marking ABS connector
Transparent Plastic Laser Marking
Transparent marking on plastic is created by using laser radiation on transparent plastics that typically have a slight colourisation to create excellent contrasting markings. Highly dependent on the material composition of these transparent parts, the markings can become darker or lighter once they have reacted with the absorbed laser marking beam.
Plastic Laser Processing
Plastic laser processing can consist of many different forms, such as cutting, peeling, drilling, or cleaning. Some of these processes are used to provide better quality, while others can eliminate the need for chemicals or other solutions.
Plastic gate cutting
Discover more about this product.
Click here to book your demo.

Major Types of Laser Marking on Plastic
When it comes to laser marking plastic, there are a few main types of processes to achieve the desired results.
Automobile instrument panel switch
Paint Peeling
Peel the paint or printing on the target surface to bring out the contrast with the colour of the base material.
(Example) Automobile instrument panel switch
Paint peeling has risen in popularity due to its simplicity and convenience. For one, conventional methods (like printing and stamping) require full plate changeovers when a design change occurs. With a laser marker, you can adjust layouts by simply changing the program. For example, in the panel switch example above, if the manufacturer wanted to print on top of the panel switch, it would require custom printing plates. Laser marking makes this task easy as it simply peels the paint off, saving both time and money.
Half cut
Surface Layer Peeling
Remove/engrave the surface layer with a laser.
(Example) Half cut
Surface layer peeling helps expose the hidden materials beneath our everyday layers, like paint, aluminite, and more. By removing these coatings with this process, a grounding point is created to better access what lies underneath. This enables new possibilities for creativity or problem-solving when it comes to marking on plastic surfaces.
A laser marker can be used to easily process a cutting section. Physical cutters are conventionally used in these scenarios but are difficult to adjust and time-consuming to change. Moreover, physical blades must be replaced often (incurring hard costs), and there's a risk that the blade will come loose and get left in the product.
Wide-area marking on LSI
Colour Development
Irradiate a plastic target with a laser to develop a colour in the target itself.
(Example) Wide-area marking on LSI
Colour development is used to create beautiful, vivid colours on plastic targets without causing any damage or engraving the material. This common technique allows for personalised customisation with creative and unique designs. Using laser radiation to develop a colour instead of engraving the plastic minimises damage from marking the target.
Welding of transparent plastic and coloured plastic
Welding
Use the heat of laser radiation to weld and join plastic parts.
(Example) Welding of transparent plastic and coloured plastic
Laser radiation welding offers a reliable and efficient way to join plastic parts, with the added benefit of no vibration, which could negatively affect the product's quality. Without making contact during the process, delicate products remain untouched, eliminating any potential imperfections or damages that may occur due to burrs.
Whatever techniques are chosen, laser marking adds clarity, precision, and visibility, making it an ideal choice for long-term results in plastic applications.
Curious about our pricing?
Click here to find out more.
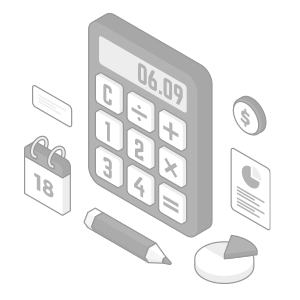
Future Trends in Plastic Laser Marking
In the past, manufacturers used printing or labeling for marking on plastic for traceability marks, barcodes, or other identifications. However, printing and labeling have adverse effects like the use of consumables and possible contamination when the mark wears off.
Now that laser marking plastic is advancing and moving faster than printing or labeling machines, machine innovations are sprouting up. Moving forward, laser marking machines are adding data storage and additional software for marking. Plastic laser marking is also taking on smaller marking shapes and sizes because of beam precision.
We’re here to provide you with more details.
Reach out today!
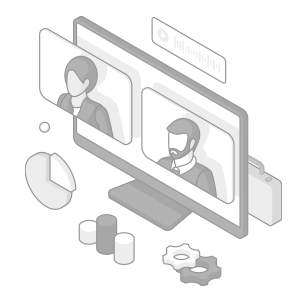