Industrial Laser Marking Systems / Laser Markers
Laser Surface Structuring Applications & Benefits
-
Tags:
- Laser Ablation , Medical , Semiconductor
Laser surface structuring is a laser ablation method that improves wettability, adhesion, friction, and grinding control. It’s used in industries like aerospace, automotive, tooling, and electric vehicle as an alternative to methods like chemical etching, sandblasting, and dot peening.
In this blog, we’ll walk you through the laser structuring process, what materials to use, applications, benefits, and how to pick your laser marking system.
How Laser Surface Structuring Works
Laser surface structuring uses a process called laser ablation. Laser ablation refers to the removal of material by an irradiated laser beam.
Laser ablation works by shooting a high-power laser beam with a short pulse onto a surface. The short pulse prevents the laser from entering the substrate while the high power evaporates or melts the target. Following laser ablation, a clean and precise surface is left behind.
We’re here to provide you with more details.
Reach out today!
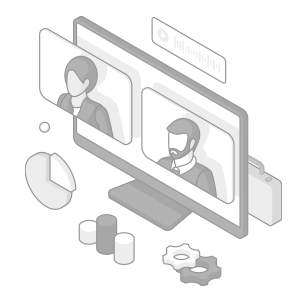
Materials Used in Laser Surface Structuring
Laser structuring is appropriate for any material: metal, plastic, ceramic, and glass.
That being said, there are different types of lasers like UV, fibre, and hybrid for different materials. Not all materials are compatible with every laser. UV lasers enable laser ablation with little to no damage, while hybrid and fibre lasers can provide the fastest cycle times.
Discover more about this product.
Click here to book your demo.

Different Laser Surface Structuring Applications
Coating Adhesion
Laser structuring improves coating adhesion significantly. In the laser structuring process, the laser will remove contaminants and oxides and form a microstructure. This microstructure is easier to stick to, due to the increased surface area, and also helps prevent contaminants and oxides from collecting on the surface in the future.
Using laser surface structuring for coating adhesion is common in the automotive, aerospace, and EV industries.
Wettability
Structured surfaces allow more control and more even distribution of liquids across their surface than bare surfaces. Typically adhesives, or other liquids, are hard to control due to the bonding within the liquid itself. This can cause pooling or lead to excess material usage.
However, using a laser to structure the surface allows for control over how the liquid rests on that surface. For instance, different shapes can be lasered on a surface and the liquid applied will remain exclusively in that area. In addition to controlling the area that the liquid is applied; it will also result in a more even distribution. This allows manufacturers to use less adhesive for a stronger bond between mating pieces.
Grinding Tools
Laser surface structuring is used to prepare grinding tools for better effectiveness when cutting grain. The precision of a laser and the micro-textures produce fewer cutting edges while preserving the strength. With fewer edges, the tool uses less force and doesn’t deform materials during the grinding process.
Friction Control
Laser structuring increases friction control on parts and components by adding rough patterns and shallow engravings. Friction control is helpful for automotive and ship brake discs.
The precision of the laser and its structures means that there’s more control over how the friction interacts with the discs and engine. With more control, there’s more effective wear and tear management. Lasers create more precise patterns than other methods like thermal spray, chemical etching, and sandblasting.
Curious about our pricing?
Click here to find out more.
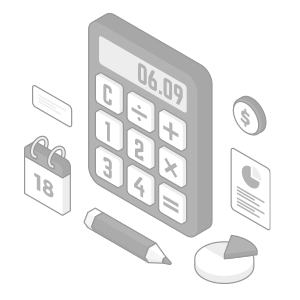
Benefits of Laser Surface Structuring
Laser structuring isn’t the first of its kind. Manufacturers have been creating structures with chemicals, gels, and sandblasting to improve adhesion, wettability, and friction for a while. However, laser structuring evolves the already used methods—chemical etching, Pasa-Jell, sandblasting—and makes them more efficient, non-toxic, and precise.
Lasers are Efficient
Laser surface structuring takes seconds to add a structure onto a surface and does not require pretreatment processes. The speed of part marking not only indicates faster structuring but also frees time for other processing and progression down the supply chain.
Alternative methods like chemical etching, sandblasting, and Pasa-Jell require pre- and post-treatments on the part that add more time. Even more, these treatments can sometimes take hours for the final result.
Lasers are Non-Toxic
Laser surface structuring does not use chemicals or other toxic consumables.
Alternative structuring methods use acids and sealants for the structuring. The disposal of these is harmful to the environment and technicians.
Lasers are Precise
Laser structuring is known for focused precision. Machines differ, but lasers can mark on the micron level. For reference, 100 micron is about the width of a human hair.
The laser’s precision contributes to the effectiveness of laser structuring applications. The more precision, the more control manufacturers have over the results.
We’re here to provide you with more details.
Reach out today!
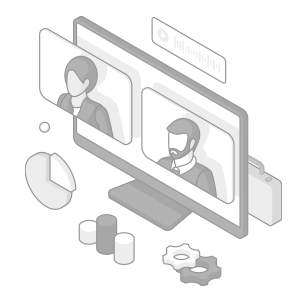
Laser Structuring Machines
Fibre laser
A fibre laser gets its name from the fibre oscillator—the optical fibre. The laser beam travels through the optical fibre and comes out as a 1090 nm infrared wavelength.
Fibre lasers have high output power, which means that their laser is powerful enough for deep engraving, fast marking, and metal projects. These lasers are also known for long service life, speed, and reliability.
UV laser
UV lasers use a process called photolytic degradation, also known as “cold marking,” with a 355 nm UV wavelength.
The 355 nm wavelength has little to no heat transfer onto the surface while still being strong enough to mark on surfaces with high heat resistance. Because of this uniqueness, a UV laser is known for its ability to mark on two ends of the spectrum—heat-resistant and heat-sensitive materials.
Curious about our pricing?
Click here to find out more.
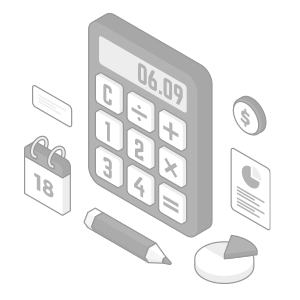
What Laser Systems are Best for Laser Structuring?
Choosing the right laser marking machine for your laser structuring involves considering your materials, versatility, type of structure, and speed.
When to Choose a Fibre Laser
Fibre lasers are known for metalworking and fast speed. If those characteristics resonate with you, then a fibre laser is the answer for you.
Other considerations for choosing a fibre laser are for deep laser marking or large production batches. If you are looking for a versatile laser that can also tackle other materials like plastics and glass, a fibre laser is not a good choice.
When to Choose a UV Laser
A UV laser is a good part marking equipment if you manufacture parts made of resin, glass, or plastic. Although UV lasers can also mark your metal components, a UV laser will not be successful for deep impressions. Therefore, if you are looking to mark metal or metal coatings with no damage then UV lasers would be the optimal choice.
When to Choose a Hybrid Laser
Hybrid lasers are a special type of laser that doesn’t fall into one “category.” Instead, these lasers combine a YVO4 laser and a fibre laser to make a hybrid. Since hybrids are not completely fibre lasers, they have more versatility.
Hybrid lasers have the strengths of a fibre laser—deep engraving, specialty in metalworking, and speed—while still having delicacy. These lasers can mark plastic and resin in addition to metal.
If you’re stuck between the UV laser and fibre laser for part marking, then a hybrid laser may be a good compromise for you.
Discover more about this product.
Click here to book your demo.

Incorporating Laser Marking Into the Manufacturing Process
Adding laser surface structuring improves your wettability, adhesion, and friction management for long-lasting components. Choosing laser structuring means that your structures will be more precise, your process will be more efficient, and your production will be environmentally friendly.
There is no one-size-fits-all answer for incorporating a laser marker into your process. That being said, there are steps you can take to find your right fit while considering your materials, batch size, and structuring goals.
Switch from contaminants and lengthy structuring processes—choose laser structuring instead.
If you need assistance deciding which of our laser marking systems is best for you, we’re here to help. KEYENCE’s 24/7 knowledgeable team is here to answer your questions about your needs and how our lasers fit with your goals. Contact us today to learn more.
We’re here to provide you with more details.
Reach out today!
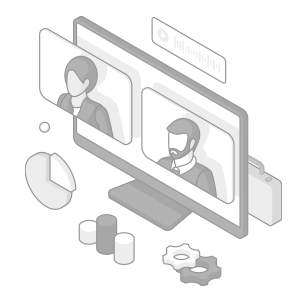