Cleanliness Inspection and Analysis of Automotive Components
Foreign particles and residue—which are known as contamination—adhering to automotive component materials and other parts, can reduce the strength and safety of products. Particularly in the automotive and aerospace industries, contamination can cause engines and other components to break, which has a direct impact on human lives, so great importance is placed on inspecting and analysing contamination and ensuring cleanliness.
This section introduces technical cleanliness inspection methods based on industrial standards, such as ISO and VDA, and the latest examples of solving problems using a 4K Digital Microscope.
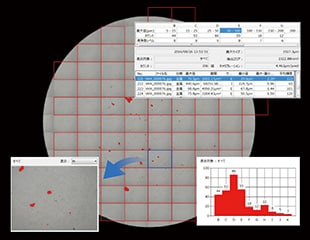
- Technical Cleanliness Inspection and Analysis in the Automotive Industry
- Solutions for Problems in Cleanliness Inspection and Analysis
- The Best Tool for Cleanliness Inspection and Analysis
Technical Cleanliness Inspection and Analysis in the Automotive Industry
All types of manufacturing sites have been inspecting and analysing contamination, foreign particles, and residue. In particular, the automotive, semiconductor, medicine, and food industries put a high importance on the cleanliness of products.
In the automotive industry, slight contamination can cause component failure or accidents, and endanger human lives. Because of this, cleanliness inspection and analysis is becoming one of the most indispensable steps in quality management.
Effects of contamination on automotive components
Pistons in automotive engines repeatedly reciprocate with a clearance of only a few micrometres and are kept air-tight with engine oil. If a slight amount of metal contamination adheres to the side surface of a piston ring, repeated reciprocation will damage the inner wall of the cylinder liner, causing engine problems.
The importance of contamination analysis has increased with the number of automobiles equipped with high-capacity batteries, such as electric vehicles (EVs), as lithium ion batteries contaminated with metal components or other particles can generate heat, or even fire.
In addition to the complete cleaning of these components after manufacturing, cleanliness analysis in compliance with international industrial standards is also required.
International industrial standards ISO 16232 and VDA 19 for technical cleanliness inspection
Cleanliness standards were introduced in the early 2000s with VDA 19 issued in 2002 by the German Association of the Automotive Industry, followed by ISO 16232 in 2007. These standards have made measurement and composition analysis of foreign particles in compliance with quality requirements mandatory.
These standards define the management of technical cleanliness for oil and water related parts, such as tanks, pumps, valves, pipes, ducts, and casing, which are used in engines and transmissions. Particle contaminants generated in the manufacturing processes of these automotive components are removed as much as possible in the cleaning process. Hence, it is necessary to perform measurements and analyses to ensure that the technical cleanliness requirements defined in ISO 16232 and VDA 19 are satisfied.
Oil has an additional international standard for cleanliness inspection, ISO 4406, which requires the counting of particles per millimetre to define how contaminants are distributed in fluids.
Methods of cleanliness inspection and analysis
There are various methods of technical cleanliness inspection and analysis, and the following two methods are defined in ISO 16232 and VDA 19 as standard technical cleanliness analysis methods for the automotive industry.
- Gravimetric method (gravimetric inspection)
- This inspection is based on weight and is thus regarded as a relatively easy method, but analysis is conducted only using information related to the difference in weights.
With this inspection, it is impossible to investigate the size of each particle contaminant, the particle size distribution, and the properties of minute particles such as metals and fibres. That means you cannot obtain information useful for determining the cause of contamination or preventing its reoccurrence.
- Light scattering method (light scattering analysis)
- Optical microscopes are used for inspection and analysis. It is possible to determine not only the presence and volume of contamination but also the size of each particle, the particle size distribution, and the properties of particles (such as metals and fibres).
In the field of automobile manufacturing where contamination by minute particles may greatly affect the quality, performance, and safety of important safety components, technical cleanliness inspection using microscopes based on this light scattering method is most common.
Flow of extracting, measuring, and analysing contamination using the light scattering method
For technical cleanliness analysis of automotive components, inspection is not possible after assembly for components such as engines, which consist of complicated and important parts. Hence, the following procedure is used to conduct analyses for each component.
- Wash the part (product) with a method such as pressure rinsing to extract foreign particles.
- Filter the rinsed liquid through a membrane filter to trap foreign particles.
- Analyse the used membrane filter as a sample using a microscope.
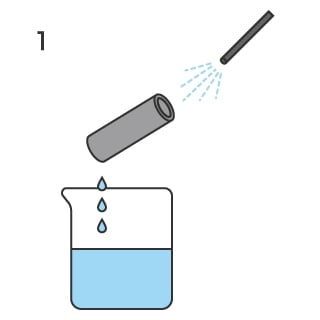
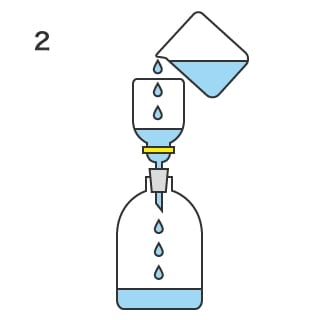
In measurement and analysis using microscopes, the number of particles (contaminant count), the particle sizes, and the type of foreign particles (such as metals and fibres) are measured, analysed, and compared under the same settings to prevent variation in measured values. Then, they are investigated in detail, including a determination of whether these items are risk factors in automotive components.
In ISO 16232 and VDA 19, various standards are defined, from methods to extract foreign particles to the minimum particle size for which analysis is required. For automatic measurement, they also define the pixel count and how to extract foreign particles. Furthermore, reports must be created in the format compliant with these standards.
Solutions for Problems in Cleanliness Inspection and Analysis
In satisfying the requirements of international standards, technical cleanliness inspection and analysis using general microscopes involve various problems, such as the skill level of the operator and the quantification of the measurement results. Also, with automatic measurement using microscopes, conditions defined in industrial standards must be met, for example, in the settings of the lens/camera (magnification and resolution), the type of lighting (brightfield, darkfield, or backlighting), and the binarisation condition (threshold) for image processing software.
These conventional problems can be solved by using KEYENCE's latest 4K Digital Microscope.
In technical cleanliness inspection and analysis, you can quickly obtain the detailed information of minute particles that conventional microscopes cannot provide. You can also reduce the time and improve the efficiency for the processes from inspection and analysis to report creation in compliance with ISO 16232 and VDA 19. Furthermore, the obtained data is useful not only to comply with the standards, but also for determining the cause of contamination, understanding trends, and improving manufacturing processes to prevent reoccurrences by saving and sharing the data.
Easy and accurate cleanliness inspection compliant with ISO 16232 and VDA
Conventional problems with microscopes
With general microscopes, technical cleanliness inspection and detailed observation as defined in industrial standards take time due to complicated settings and require a certain level of proficiency to obtain accurate analysis results.
With the VHX Series 4K Digital Microscope
The VHX Series enables users to carry out cleanliness inspections compliant with the ISO 16232 and VDA 19 standards for the automotive industry. By analysing a high-resolution image with a deep depth of field taken with the 4K Digital Microscope, even targets with uneven surfaces can be measured with high accuracy.
Cleanliness inspection can be performed automatically with a few clicks. After the inspection is ran, the operator can use Detailed Analysis mode to further investigate particles and analyse their cause.
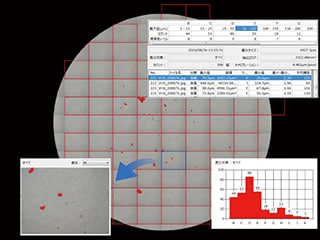
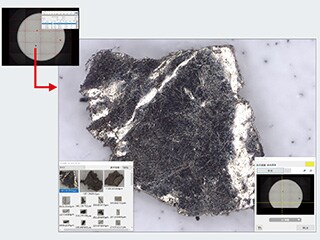
Automatic inspection settings improves results and speed
Conventional problems with microscopes
With a conventional microscope, it is impossible to accurately reproduce imaging conditions (lighting, exposure time, white balance) every time. Additionally, it is possible for users to select the incorrect lens for analysis, requiring the test to be repeated.
With the VHX Series 4K Digital Microscope
The VHX Series automatically reproduces imaging settings from past results, ensuring there is no variation due to inconsistent lighting, magnification, or white balance. The ability to automate the process not only educes work hours, but also eliminates different operators obtaining different values.

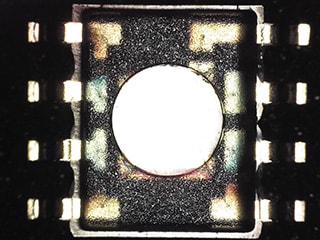
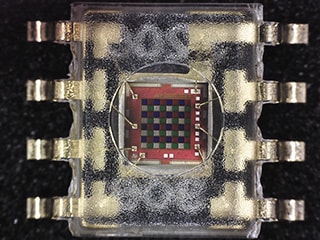
The high-resolution HR lens and motorised revolver enable a seamless zoom function that quickly switches lenses from 20x to 6000x magnification according to the size of contamination, eliminating the need for lens replacement. Additionally, the VHX Series automatically identifies the connected lens and records the magnification data with the captured image.
Finally, the VHX Series offers automatic calibration with just the click of a button, ensuring user results are accurate.
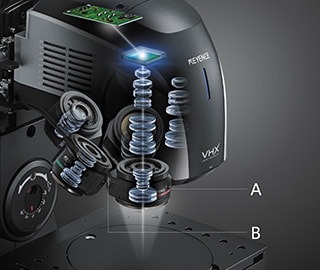
- A. High-resolution HR lens
- B. Motorised revolver
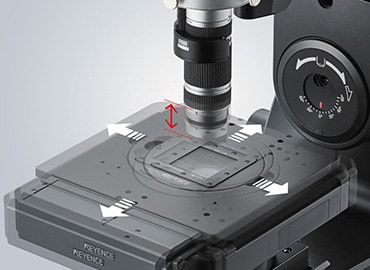
The Best Tool for Cleanliness Inspection and Analysis
The VHX Series high-definition 4K Digital Microscope offers excellent efficiency compared to conventional microscopes and makes it possible to eliminate human errors and ensure accurate cleanliness inspection and analysis.
The high-definition 4K images allow for clear and detailed observation of minute particles, producing quick and sophisticated analysis results.
The captured or measured data can be easily output as a report with a fixed format. Sharing this data via an intranet server can be useful not only for quality assurance and ensuring conformity with industrial standards, but also for identifying the causes of contamination and for process improvement.
Equipped with many other advanced functions, the VHX Series is a powerful partner for ensuring cleanliness of products. For additional product info or inquiries, click the buttons below.